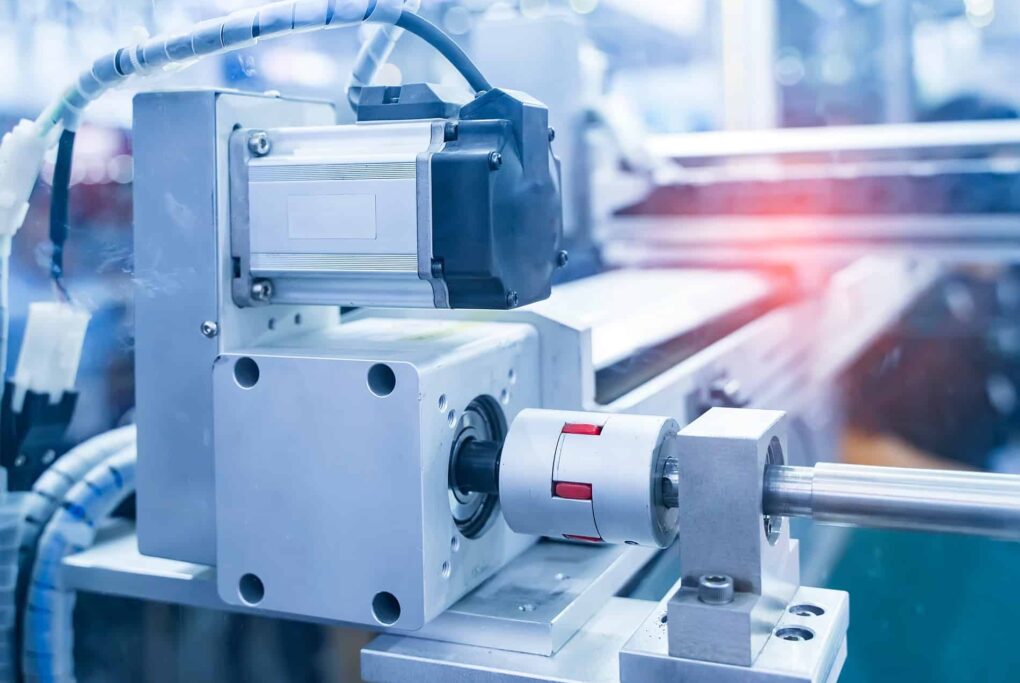
Na pierwszy rzut oka silnik krokowy i serwonapęd mogą wydawać się podobnymi urządzeniami. Zarówno jeden jak i drugi wariant nie posiada szczotek oraz wymaga do pracy specjalnego sterownika. Jednakże pomimo kilku wspólnych cech, w większości przypadków nie można stosować tych urządzeń zamiennie. Poniżej wymienione zostały cechy obu napędów, ich zastosowania oraz różnice między nimi.
Serwonapęd a silnik krokowy – różnice
Zarówno silniki krokowe, jak i serwonapędy składają się z dwóch podstawowych elementów: silnika i sterownika, którego zadaniem jest zarządzanie energią dostarczaną do silnika przez przychodzący sygnał sterujący.
Silniki krokowe wykonują ruch obrotowy, który podzielony jest na kroki. Pojedynczy krok stanowi zwykle niewielką część kąta pełnego, np 1,8°, 2°, 5°. Silnik taki nie obraca się płynnie, tylko wykonuje skoki pomiędzy krokami, dlatego też dobrze sprawdza się pracując w trybie pozycyjnym, a jednocześnie nie nadaje się do płynnej pracy ciągłej.
Silnik serwo swoją konstrukcją przypomina silnik BLDC. W tej konstrukcji, ruch wirnika jest efektem częstotliwości, polaryzacji, fazy i wartości dostarczanego prądu, za co odpowiada serwosterownik.
Różnica między tymi dwoma rodzajami napędów polega również na sposobie sterowania. Silnik krokowy pracuje w otwartej pętli sprzężenia zwrotnego oraz ma możliwość pracy w zamkniętej pętli.
Serwonapęd może pracować wyłącznie w pętli zamkniętej sprzężenia zwrotnego. Z tego powodu, każdy silnik serwo posiada enkoder, którego zadaniem jest śledzenie pozycji i prędkości, a następnie dostosowywanie na ich podstawie parametrów zasilania.
W przypadku serwonapędów podaje się moc silnika, natomiast w przypadku silników krokowych – moment (Ncm lub Nm).
Silnik krokowy i serwonapęd – zastosowanie
Zarówno silniki krokowe, jak i serwonapędy służą do precyzyjnego sterowania ruchem. Serwonapędy umożliwiają sterowanie prędkością i momentem. W przeciwieństwie do silników krokowych są przystosowane do pracy ciągłej. Oferują możliwość przełączania między sterowaniem pozycją, prędkością i momentem. W silnikach krokowych zauważalny jest za to spadek momentu obrotowego wraz ze wzrastającą prędkością obrotową.
Serwonapędy w przemyśle najczęściej wykorzystywane są do:
- pakowania,
- dozowania,
- butelkowania,
- etykietowania,
- transportu materiałów,
- obróbki materiałów,
- montażu materiałów.
Silniki krokowe w przemyśle najczęściej znajdują zastosowanie w:
- drukarkach 3D,
- maszynach CNC,
- urządzeniach laboratoryjnych,
- mieszalnikach farb,
- robotach przemysłowych.
Czy silnik krokowy może zastąpić serwonapęd?
W niektórych zastosowaniach, w pewnym zakresie czynności może. Na rynku dostępne są silniki krokowe przeznaczone do ciągłej kontroli prędkości. Takie rozwiązanie będzie dobrą alternatywą dla serwonapędu ze względu na mniejsze gabaryty i wagę. Niektóre silniki krokowe pozwalają na pracę w zamkniętej pętli i możliwość sterowania momentem. Dzięki temu możliwe staje się zastosowanie silników krokowych do zastosowań wymagających przyłożenia siły o konkretnej wartości.
Serwonapęd a silnik krokowy – podsumowanie
Zastosowanie, wymagania i budżet – to podstawowe czynniki, które determinują wybór serwonapędu lub silnika krokowego. Nie biorąc pod uwagę tych parametrów, nie da się jednoznacznie stwierdzić, które rozwiązanie jest lepsze.
Zalety silników krokowych:
- Prosta budowa i łatwe sterowanie.
- Nie wymaga sygnału zwrotnego – praca w otwartej pętli.
- Osiągają wysoki moment przy niskich prędkościach.
- Przystępne cenowo.
Wady silników krokowych:
- Wraz ze wzrostem prędkości spada ich moment.
- Brak reakcji na zmiany w obciążeniu.
Zalety serwonapędów:
- Posiadają sprzężenie zwrotne.
- Oferują stały moment.
- Niewielkie nagrzewanie się i cicha praca.
- Idealne do aplikacji ze zmiennym obciążeniem.
Wady serwonapędów:
- Skomplikowane sterowanie wymagające precyzyjnej regulacji.
- Wysoki koszt.